2018年8月の第1製造部(古川工場)の5S活動事例を紹介します。
第1製造部では「ACM粉砕ローター専用工具BOXの製作」を実施しました。
<改善前の状態&問題点>
ACM粉砕ローター、専用工具がボックスに乱雑に入れられている為、見た目も悪く、運搬の際などに粉砕ローターの刃などが工具とぶつかり傷ついてしまう恐れがありました。また、紛失の際など分かりにくい状態でした。
<改善後の状態&効果>
スポンジで定位置管理できるように専用の型を作成しました。これにより見た目が良く、工具や部品の片付けが容易になり、損傷防止に繋がりました。また、紛失した場合など一目でわかるようになりました。
2018年8月の総務部(古川工場)のKY活動事例を紹介します。
以下の作業をテーマとして取り上げ、KYT(危険予知訓練)を実施しました。
テーマ
道路沿いの草刈りと補助作業
1ラウンド:どんな危険が潜んでいるか?
2ラウンド:これが危険ポイントだ!
以下の危険が挙げられ、重要危険ポイントを設定しました。
◎ |
1 |
道路沿いの草刈りと補助作業をする時は、安全反射ベストを着用しないと通行車両に認識されるのが遅れる。 |
◎ |
2 |
草刈り作業者と補助作業者の距離が近いと、小石が飛び跳ねて補助作業者の体に当たり怪我をする。 |
◎ |
3 |
草刈り作業者は地面を見ながら作業をする為、電柱等の障害物に気がつくのが遅れ刈払機をスライドさせた時、障害物に接触する。 |
○ |
4 |
草刈り作業者は地面を見ながら作業をする為、歩行者に気がつくのが遅れ小石が飛び跳ねて歩行者に当たり怪我をする。 |
◎:最重要危険ポイント/○:重要危険ポイント
3ラウンド:あなたならどうする?
上記の◎最重要危険ポイントに対して、以下の具体的対策案が提案されました。
※ |
1 |
道路沿いの草刈り作業と補助作業は必ず安全反射ベストを着用して作業する。 |
※ |
2 |
草刈り作業者と補助作業者は8m程度の距離を空けて、作業中は距離間を保つ。 |
※ |
3 |
草刈り作業開始前に、障害物がどこにあるのかを確認しておく。 |
※:重点実施項目
4ラウンド:私たちはこうする!
上記の対策案を実施するために、以下のチーム行動目標と指差し呼称を設定しました。
チーム行動目標 |
障害物を確認し、安全反射ベストを着用し、2人の距離間を保ちながら作業しよう。 |
指差し呼称 |
障害物確認、ヨシ!安全反射ベスト着用、ヨシ!距離間ヨシ、! |
2018年8月の設備保全部(古川工場)のKY活動事例を紹介します。
以下の作業をテーマとして取り上げ、KYT(危険予知訓練)を実施しました。
テーマ
ジグソーでの盤加工
1ラウンド:どんな危険が潜んでいるか?
2ラウンド:これが危険ポイントだ!
以下の危険が挙げられ、重要危険ポイントを設定しました。
◎ |
1 |
保護具をしていないと切削粉やバリで目や指を痛める。 |
◎ |
2 |
加工物が安定してないと切削中、ジグソーの刃が噛んで折れ指等を痛める。 |
○ |
3 |
無理な姿勢で作業すると腰を痛める。 |
◎:最重要危険ポイント/○:重要危険ポイント
3ラウンド:あなたならどうする?
上記の◎最重要危険ポイントに対して、以下の具体的対策案が提案されました。
※ |
1 |
保護具を着用(メガネ、手袋)。 |
※ |
2 |
加工物は安定を確認してから作業する。 |
※:重点実施項目
4ラウンド:私たちはこうする!
上記の対策案を実施するために、以下のチーム行動目標と指差し呼称を設定しました。
チーム行動目標 |
ジグソーでの加工は加工物の安定を確かめて保護具を着用して作業しよう |
指差し呼称 |
(対象物に対して)安定よし、保護具よし |
2018年8月の原料課(古川工場)のKY活動事例を紹介します。
以下の作業をテーマとして取り上げ、KYT(危険予知訓練)を実施しました。
テーマ
トラックシート ゴムかけ作業
1ラウンド:どんな危険が潜んでいるか?
2ラウンド:これが危険ポイントだ!
以下の危険が挙げられ、重要危険ポイントを設定しました。
◎ |
1 |
ゴムを掛け忘れると、運搬中シートが外れ荷物が落下し、事故につながる。 |
○ |
2 |
タイヤ付近のゴムを掛け忘れ、ぶら下がった状態になっていると、運搬中タイヤに巻き込まれ事故につながる。 |
◎ |
3 |
ゴムが劣化していると、引っ張った時に切れて、顔や体に当たりケガをする。 |
◎:最重要危険ポイント/○:重要危険ポイント
3ラウンド:あなたならどうする?
上記の◎最重要危険ポイントに対して、以下の具体的対策案が提案されました。
※ |
1 |
ゴムを掛ける度に張り具合をチェックし、掛け終わったあと全体をもう一度回ってチェックする。 |
※ |
2 |
ゴムの状態を確認してから作業する。 |
※:重点実施項目
4ラウンド:私たちはこうする!
上記の対策案を実施するために、以下のチーム行動目標と指差し呼称を設定しました。
チーム行動目標 |
ゴムを掛ける時は、張り具合・長さ・状態を確認してから作業し、最後にもう一度全体を確認しよう。 |
指差し呼称 |
ゴム状態よし!全体よし! |
2017年7月の「配管フェルール化を進行中/パッキン混入リスクゼロを目指します!」の中でご紹介しました古川受託粉砕部門の「配管の完全フェルール化2カ年計画」の途中経過としまして、この度、社内で規格化されている配管についてはフェルール化が完了しました。
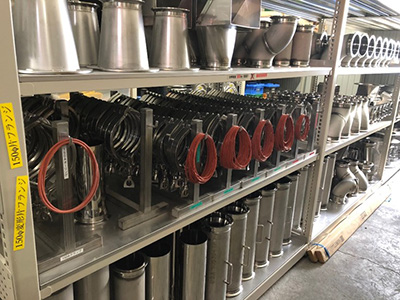
配管フェルール化とは
当社の受託粉砕の粉砕プラントを大雑把に表すと原料ホッパー、粉砕機、回収機から成っています。これらの設備は複数の配管で連結されており、その中を粉体が通って送られるようになっています。
従来はフランジ継手の配管を使っておりましたが、フランジ継手の配管を接続するためには接続部にパッキンを使用する必要がありました。その為、パッキンが劣化していたりすると通過する粉体との接触によって削れて混入するリスクがありました。
このリスクを無くすためにパッキンを使用しないフェルール継手の配管に変更していこうという活動が配管フェルール化です。
社内規格配管のフェルール化が完了
昨期から順次フェルール化を進めてきて、この度、社内で規格化されている配管についてはすべてフェルール化することができました。フェルール化した配管の数は200本にのぼります。
社内規格配管がすべてフェルール継手なったことで、大多数の粉砕プラントでは配管の接続部にパッキンが使われることがなくなり、長年抱えていたパッキン混入リスクがゼロに近づきました。
完全フェルール化を達成し今以上に安心できる製品をお客様に
2カ年計画の完了期日は今期末です。今後は規格化されていない配管についてもフェルール化を推し進めていき、今期末までには完全フェルール化を達成できるようにしていきます。
完全フェルール化を達成しパッキン混入リスクをゼロとすることで、今まで以上に安心できる製品をお客様にお届けできるようにしていきます。
製品回収率の向上を狙い、粉体回収機ホッパー部の改良をしました。まずは古川工場の粉体回収機1台を対象に、試験的に実施しました。
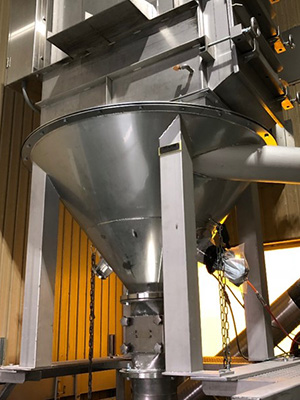
改良後の円錐型ホッパー部
従来の粉体回収機の課題
当社では粉砕した粉体製品を回収するためにバグフィルターを内部に持つ粉体回収機を使用しています。その粉体回収機の内部には粉体が付着し残留するので、製品回収率が低下するという課題が過去からあります。
粉体が回収機内に残留する箇所としては、バグフィルター、回収機側面、回収機下部のホッパー部ですが、今回はホッパー部に注目して改良をしました。
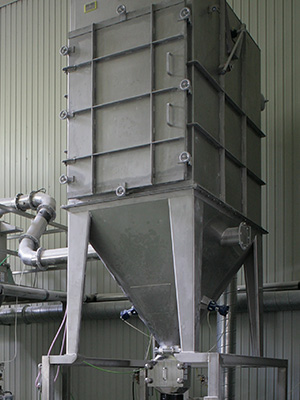
従来の四角錐型ホッパー部
ホッパー部分を逆円錐型に改良
従来の粉体回収機のホッパー部は逆四角錐型をしています。その角部に粉体が溜まりやすいとの考察結果から、角部のないホッパーにすれば粉体がスムーズに落ちていき、残留も減るだろうと考えました。
そこで試験的に製作したのが円錐型のホッパーです。
製品回収率向上を実感
円錐型のホッパーを取り付けた粉体回収機を使って製造したところ、現状では回収率を数字では評価してはいないものの、製造現場の実感としては上々とのことです。製造完了後に回収機を分解してホッパー部を確認した際の粉体の残留状況や、ホッパー部を洗浄する際の洗浄のしやすさからも実感できているようです。
今回改良したものによる評価も引き続き実施しながら、他の粉体回収機への展開も予定しており、多くの製品の回収率向上に繋げていきたいと考えています。
<品種・材料/粒子径>
天産物の粉砕/Dp50
<管理図の変化>
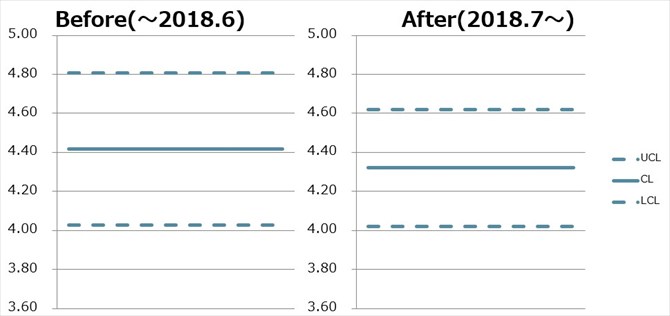
(単位:µm)
<改善内容>
粉砕機内の原料が最適量で安定するように調整しました。
※当社のノウハウとなる部分につきましては、抽象的な表現にさせていただいています。ご了承ください。