2023年6月の第2製造部(古川工場)のKY活動事例を紹介します。
以下の作業をテーマとして取り上げ、KYT(危険予知訓練)を実施しました。
テーマ
4-8室スクラバー炭酸カリウム投入作業
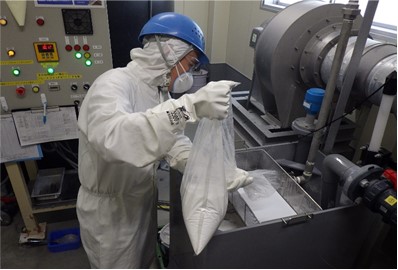
1ラウンド:どんな危険が潜んでいるか?
2ラウンド:これが危険ポイントだ!
以下の危険が挙げられ、重要危険ポイントを設定しました。
○ |
1 |
投入ザルを使用せずに炭酸カリウムを投入すると、スクラバー液が跳ね返り皮膚に付着し荒れる。 |
◎ |
2 |
保護手袋を着用せずに炭酸カリウムを扱うと皮膚に付着して皮膚が荒れる。 |
◎ |
3 |
保護マスクを着用せずに炭酸カリウムを扱うと、鼻や口から吸引し体内に入り込み体調不良になる。 |
◎ |
4 |
保護メガネを着用せずに炭酸カリウムを投入すると、飛散した際に目に入り炎症を起こす。 |
◎:最重要危険ポイント/○:重要危険ポイント
3ラウンド:あなたならどうする?
上記の◎最重要危険ポイントに対して、以下の具体的対策案が提案されました。
※ |
1 |
炭酸カリウムを扱う際は保護手袋を着用する。 |
※ |
2 |
炭酸カリウムを扱う際は保護マスクを着用する。 |
※ |
3 |
炭酸カリウムを扱う際は保護メガネを着用する。 |
※:重点実施項目
4ラウンド:私たちはこうする!
上記の対策案を実施するために、以下のチーム行動目標と指差し呼称を設定しました。
チーム行動目標 |
炭酸カリウムを扱う際は必ず決められた保護具を着用しよう。 |
指差し呼称 |
保護具よし! |
2023年6月の設備保全部(古川工場)のKY活動事例を紹介します。
以下の作業をテーマとして取り上げ、KYT(危険予知訓練)を実施しました。
テーマ
ハンドグラインダー作業
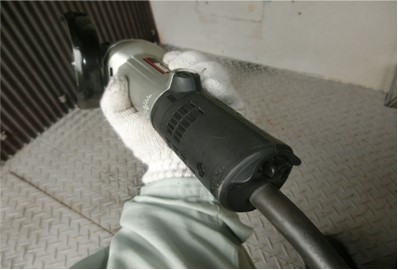
1ラウンド:どんな危険が潜んでいるか?
2ラウンド:これが危険ポイントだ!
以下の危険が挙げられ、重要危険ポイントを設定しました。
◎ |
1 |
電源コンセントを挿したときにスイッチがオンになっているといきなり回り出し、身体に刃が触れているとケガをする。 |
○ |
2 |
濡れた手で電源コンセントを挿すと感電する。 |
◎ |
3 |
刃の固定ナットが緩んでいると刃のバランスが崩れ思わぬケガをする。 |
○ |
4 |
片手で作業をすると安定が悪く、グラインダーが跳ねてケガをする。 |
◎:最重要危険ポイント/○:重要危険ポイント
3ラウンド:あなたならどうする?
上記の◎最重要危険ポイントに対して、以下の具体的対策案が提案されました。
※ |
1 |
電源コンセントを入れる前にスイッチがオフになっているか目視確認する。 |
※ |
2 |
使用前に刃を手で回して固定されているか確認する。 |
※:重点実施項目
4ラウンド:私たちはこうする!
上記の対策案を実施するために、以下のチーム行動目標と指差し呼称を設定しました。
チーム行動目標 |
ハンドグラインダーの使用前に刃の固定は良いか、スイッチはオフになっているか確認しよう。 |
指差し呼称 |
刃の固定よし!スイッチオフよし! |
2022年6月の製造部(本社)の5S活動事例を紹介します。
製造部では「第3工場掃除道具置き場の改善」を実施しました。
<改善前の状態&問題点>
第3工場にある掃除道具は、特定の収納場所が決まっておらずフック等で引掛けておくだけの状態となっていました。
<改善後の状態&効果>
工場内の壁に掃除道具ごとのキャッチャーやフック取り付け、決められた場所に収納できるようにしました。定置管理され道具も収納しやすく整理整頓された状態となりました。
2022年6月の第2製造部(古川工場)のKY活動事例を紹介します。
以下の作業をテーマとして取り上げ、KYT(危険予知訓練)を実施しました。
テーマ
棚型ラック運搬作業
(リーチリフト使用)
1ラウンド:どんな危険が潜んでいるか?
2ラウンド:これが危険ポイントだ!
以下の危険が挙げられ、重要危険ポイントを設定しました。
○ |
1 |
リーチリフトは通常のリフトと操作方法が異なる為、操作に気を取られていると、周囲にいる作業者に接触しケガをさせる。 |
◎ |
2 |
通路が狭いためリフトの運転に集中しすぎると、付近を通行する歩行者に接触しケガをさせる。 |
|
3 |
フォークが水平では無い状態で運搬を行うと、トレイが落下して周囲の作業者に当たりケガをさせる。 |
◎ |
4 |
ラックばかりに気を取られ周囲の安全確認を怠ると、運搬する際、歩行者に接触しケガをさせる。 |
◎:最重要危険ポイント/○:重要危険ポイント
3ラウンド:あなたならどうする?
上記の◎最重要危険ポイントに対して、以下の具体的対策案が提案されました。
※ |
1 |
運搬する前に周囲に作業者・歩行者がいないことを確認する。 |
※:重点実施項目
4ラウンド:私たちはこうする!
上記の対策案を実施するために、以下のチーム行動目標と指差し呼称を設定しました。
チーム行動目標 |
ラックを運搬する際には周囲の安全を確認しながら運転しよう。 |
指差し呼称 |
周囲安全よし |
2022年6月の設備保全部(古川工場)のKY活動事例を紹介します。
以下の作業をテーマとして取り上げ、KYT(危険予知訓練)を実施しました。
テーマ
ベアリングヒート作業
1ラウンド:どんな危険が潜んでいるか?
2ラウンド:これが危険ポイントだ!
以下の危険が挙げられ、重要危険ポイントを設定しました。
◎ |
1 |
素手でベアリングに触ると高温のため火傷する(約100℃) |
◎ |
2 |
熱に弱い素材の手袋で作業すると手袋が溶け火傷する。 |
○ |
3 |
ベアリング運搬時、周囲を良く確認しないとベアリングを他の作業者に接触させ火傷する。 |
◎:最重要危険ポイント/○:重要危険ポイント
3ラウンド:あなたならどうする?
上記の◎最重要危険ポイントに対して、以下の具体的対策案が提案されました。
※ |
1 |
軍手を着用して作業する。 |
※ |
2 |
周囲を把握して移動する。 |
※:重点実施項目
4ラウンド:私たちはこうする!
上記の対策案を実施するために、以下のチーム行動目標と指差し呼称を設定しました。
チーム行動目標 |
ベアリングヒート時は必ず軍手を着用し周囲を確認してから移動しよう。 |
指差し呼称 |
軍手着用よし!周囲よし! |
2022年4月の第2製造部(古川工場)の5S活動事例を紹介します。
第2製造部では「梱包用具置き場の設置」を実施しました。
<改善前の状態&問題点>
製品梱包をローラー台を使用して行う際、テープカッターや、ウエス、PPタイの置き場がありません。その為、不要なファイバードラムを利用し置き場として使用しています。
<改善後の状態&効果>
ローラー台に、ステンレス製で梱包用具を置ける台を設置しました。設置した事により作業効率が向上した事と、ローラー台の上部を有効活用出来るようになりました。
2022年4月の総務部(古川工場)のKY活動事例を紹介します。
以下の作業をテーマとして取り上げ、KYT(危険予知訓練)を実施しました。
テーマ
可燃ゴミ積載作業
1ラウンド:どんな危険が潜んでいるか?
2ラウンド:これが危険ポイントだ!
以下の危険が挙げられ、重要危険ポイントを設定しました。
◎ |
1 |
可燃ゴミを軽トラに積載する時、足腰に負担がかかる。 |
◎ |
2 |
可燃ゴミを軽トラに積載する時、ゴミが重いので片手で持ち上げると体を痛める。 |
○ |
3 |
可燃ゴミを軽トラに積載した後、シートをしっかりかけて走行しないと、ゴミが荷台から落下する。 |
◎:最重要危険ポイント/○:重要危険ポイント
3ラウンド:あなたならどうする?
上記の◎最重要危険ポイントに対して、以下の具体的対策案が提案されました。
※ |
1 |
可燃ゴミを軽トラに積載する時は、腰痛ベルトと手袋を着用して行う。 |
※ |
2 |
可燃ゴミを持ち上げる時は、両手で持ち上げる。 |
|
3 |
作業者が2人いる場合は、下から荷台上へ受け渡しの2人作業で行う。 |
※:重点実施項目
4ラウンド:私たちはこうする!
上記の対策案を実施するために、以下のチーム行動目標と指差し呼称を設定しました。
チーム行動目標 |
可燃ゴミを軽トラに積載する時は、保護具を着用し両手で持ち上げよう。 |
指差し呼称 |
両手持ち、保護具着用ヨシ! |