2014年12月の第2製造部(古川工場)のKY活動事例を紹介します。
以下の作業をテーマとして取り上げ、KYT(危険予知訓練)を実施しました。
テーマ
粉体回収用フレコンの交換作業
1ラウンド:どんな危険が潜んでいるか?
2ラウンド:これが危険ポイントだ!
以下の危険が挙げられ、重要危険ポイントを設定しました。
◎ |
1 |
制御盤の4ヶ所のスイッチを切り忘れてフレコン取り外し作業を行うと、粉が噴き出して作業者の目に入る。 |
◎ |
2 |
洗浄品の取り出し口にカバーを付け忘れて作業を行うと、フレコン交換作業中に微粉が目に入る。 |
○ |
3 |
フレコン止めバンドは稼働中外れないようにきつく巻いてある為、注意せずに外すとバンドが勢いよく外れ作業者に当たる。 |
○ |
4 |
洗浄品の取り出し口は少し高い位置にある為パレットに乗って作業を行うが、作業に集中すると足を踏み外し足をぶつける。 |
◎:最重要危険ポイント/○:重要危険ポイント
3ラウンド:あなたならどうする?
上記の◎最重要危険ポイントに対して、以下の具体的対策案が提案されました。
※ |
1 |
フレコン交換時は制御盤の4ヶ所のスイッチを確実に切る。 |
※ |
2 |
洗浄品取り出し口のカバーを付けてから作業を行う。 |
※:重点実施項目
4ラウンド:私たちはこうする!
上記の対策案を実施するために、以下のチーム行動目標と指差し呼称を設定しました。
チーム行動目標 |
フレコン交換時は、制御盤の4ヶ所のスイッチを必ず切り、取り出し口のカバーを付けてから作業を行おう! |
指差し呼称 |
スイッチよし!カバーよし! |
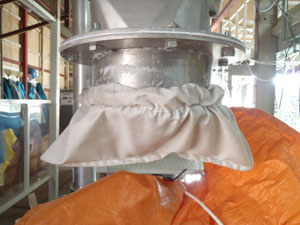
取り出し口カバー
2014年12月の第1製造部(古川工場)のKY活動事例を紹介します。
以下の作業をテーマとして取り上げ、KYT(危険予知訓練)を実施しました。
テーマ
高所作業リフター使用作業
1ラウンド:どんな危険が潜んでいるか?
2ラウンド:これが危険ポイントだ!
以下の危険が挙げられ、重要危険ポイントを設定しました。
◎ |
1 |
アウトリガーを掛けないで昇降作業を行うと、作業車が傾き、横転する。 |
◎ |
2 |
アウトリガーを掛けないでバケット内で作業を行うと、横揺れしたときに作業車が傾き横転する。 |
◎ |
3 |
アウトリガーのロックピンを掛けずに使用すると、作業のはずみでアウトリガーが緩み、作業車が傾き横転する。 |
○ |
4 |
4ヶ所のアウトリガーを掛けずに作業を行うと、掛かっていない方向に横揺れし、弾みで転倒する。 |
◎:最重要危険ポイント/○:重要危険ポイント
3ラウンド:あなたならどうする?
上記の◎最重要危険ポイントに対して、以下の具体的対策案が提案されました。
※ |
1 |
4ヶ所あるアウトリガーを全て掛け、ロックピンも掛かっていることを確認してから作業を行う。 |
※:重点実施項目
4ラウンド:私たちはこうする!
上記の対策案を実施するために、以下のチーム行動目標と指差し呼称を設定しました。
チーム行動目標 |
4ヶ所あるアウトリガーを全て掛け、ロックピンも掛かっているか確認してから作業しよう。 |
指差し呼称 |
アウトリガーよし!ロックピンよし! |
古川工場に自動床洗浄機を導入しました。
当社では数年前から、工場内の粉砕室、通路、倉庫の床に防塵塗装を施してきました。この防塵塗装のおかげで、粉が床に舞い落ちても掃除がしやすい環境となっており、作業者は時間を見つけてはモップでさっと床掃除をして、綺麗な状態を保つことが習慣となっています。
この床掃除をもっと効率化するために、今回、自動床洗浄機を導入しました。
一品番の粉砕が終わった後などは、粉砕設備が解体され粉砕室から一掃されるので、この自動床洗浄機が見事に力を発揮し、モップよりも綺麗にスピーディーに床を掃除をすることができるようになりました。
スキマ時間にはモップ、広範囲を一度に掃除するときには自動床洗浄機、両方をうまく使いながら工場内を綺麗に保つようにしています。
「粉を扱う工場なのに、粉がぜんぜん落ちていませんね。」
工場にいらっしゃった方には、このように言っていただけるように常日頃、床掃除には気を配っています。
古川工場に高所作業リフターを導入しました。
古川工場には従来から高所作業車はありましたが、高所作業車を使用するには特別教育を修了していなければならず、使用できる者が限られていました。
今回、導入した高所作業リフターは自走せず人の手で移動させる方式であり、特別教育を受講する必要がありません。そのため、高所作業をしたい人が自ら持ち出してすぐに使うことができ、今までよりも効率的に作業を進めることができるようになりました。
古川工場の品質保証部製品管理課に「マワールでんラッパー」を導入しました。
マワールでんラッパーとは、パレットに積み上げた製品を半自動でシュリンク包装できるストレッチ包装機です。
導入の主な目的は、作業者の腰痛を予防することです。
マワールでんラッパーを導入する前は、作業者がシュリンクフィルムの筒を持って、積み上げられた製品の周囲をぐるぐると何周か歩いて回って包装していました。このとき、中腰の状態で歩いて回らなくてはならず、作業者の腰に負担がかかっていました。多いときには一日に30パレット以上のシュリンク包装をしているので、腰への負担は小さくはありませんでした。
導入したマワールでんラッパーは、ペダルを踏むことで、ターンテーブルに載せたパレット、製品を自動で回転させることができます。そのため、作業者はシュリンクフィルムの筒を持って中腰で歩き回る必要がなくなり、腰への負担は非常に小さくなりました。
2014年11月の開発部(古川工場)の5S活動事例を紹介します。
今回、開発部では工具の管理方法を改善しました。
<改善前の状態&問題点>
C-1室を開発部で使用する様になったため壁掛けを利用し必要最小限の工具を揃えました。
しかし工具を揃えたままで個々の形跡線も無く、一つのフックに同じサイズのスパナが二つ掛かっていたり、一つのフックに複数の工具が掛かっている状態であったため、工具が無くなっても気づかない可能性がありました。
<改善後の状態&効果>
台車を購入し青色スポンジを各工具の形に切り抜き、工具を設置するようにしました。
これによって、工具が無くなっている場合にはひと目でわかる状態となり、員数・定置管理が容易にできるようになりました。
2014年11月の製造部(本社)のKY活動事例を紹介します。
以下の作業をテーマとして取り上げ、KYT(危険予知訓練)を実施しました。
テーマ
高所架台への原料搬入作業
1ラウンド:どんな危険が潜んでいるか?
2ラウンド:これが危険ポイントだ!
以下の危険が挙げられ、重要危険ポイントを設定しました。
○ |
1 |
原料を架台に載せた後、バックする際、フォークリフトの爪がパレットに引っかかりドラムが落下し、他の作業者に当たり怪我をする |
○ |
2 |
原料を架台に載せる際、フォークリフトが柱などに当たり、ドラムが落下し、他の作業者に当たり怪我をする |
◎ |
3 |
バックする際、荷に気をとられ、後方の作業者にぶつかり怪我をする |
○ |
4 |
マストを後傾させすぎると、ドラムがずれ落ち、作業者に当たり怪我をする |
|
5 |
架台の上に、作業者がいる事に気づかず、搬入し作業者に当たり怪我をする |
◎:最重要危険ポイント/○:重要危険ポイント
3ラウンド:あなたならどうする?
上記の◎最重要危険ポイントに対して、以下の具体的対策案が提案されました。
※ |
1 |
バックする際は、確実に後方確認、周囲確認を実施する |
※ |
2 |
確認する際は、指差し呼称実施 |
※:重点実施項目
4ラウンド:私たちはこうする!
上記の対策案を実施するために、以下のチーム行動目標と指差し呼称を設定しました。
チーム行動目標 |
バックする際は、後方、周囲確認を、指差し呼称で確実に実施し作業しよう |
指差し呼称 |
後方、周囲確認ヨシ! |