2025年1月の原料部(古川工場)のKY活動事例を紹介します。
以下の作業をテーマとして取り上げ、KYT(危険予知訓練)を実施しました。
テーマ
選別室からのフレコン搬出作業
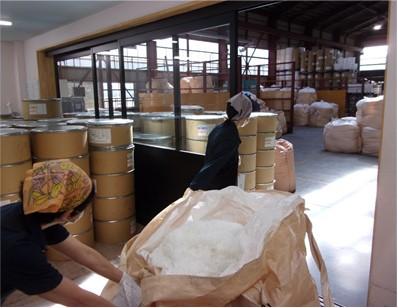
1ラウンド:どんな危険が潜んでいるか?
2ラウンド:これが危険ポイントだ!
以下の危険が挙げられ、重要危険ポイントを設定しました。
◎ |
1 |
慌てたり急いでいる時、力強く扉を開けると反対側にいる人や物に当たり怪我をする。 |
○ |
2 |
完全に扉が開けきれてないまま選別室からフレコンを出そうとすると、台車と扉で板挟みになり怪我をする。 |
|
3 |
両サイドから同時に扉を開けると手を挟んだり体に当たり怪我をする。 |
◎:最重要危険ポイント/○:重要危険ポイント
3ラウンド:あなたならどうする?
上記の◎最重要危険ポイントに対して、以下の具体的対策案が提案されました。
※ |
1 |
扉を開ける時は慌てずゆっくりと開け、反対側で作業している人がいたら声を掛けてから開ける。 |
※:重点実施項目
4ラウンド:私たちはこうする!
上記の対策案を実施するために、以下のチーム行動目標と指差し呼称を設定しました。
チーム行動目標 |
扉を開ける時は慌てずゆっくりと開け、反対側で作業している人がいたら声を掛けてから開けよう。 |
指差し呼称 |
扉、作業者確認よし |
2025年1月の開発部(古川工場)のKY活動事例を紹介します。
以下の作業をテーマとして取り上げ、KYT(危険予知訓練)を実施しました。
テーマ
アルミフレーム組立作業
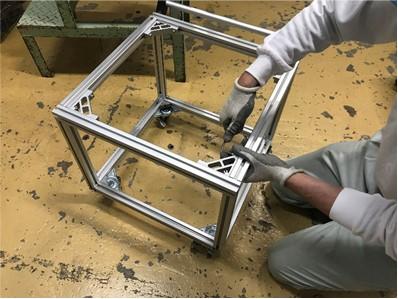
1ラウンド:どんな危険が潜んでいるか?
2ラウンド:これが危険ポイントだ!
以下の危険が挙げられ、重要危険ポイントを設定しました。
◎ |
1 |
アルミフレームは切断された状態で角が立っており、組み立てる際、手を傷つける。 |
◎ |
2 |
固定ブラケットの残りバリに気付かず、組み立てる際、けがをする。 |
◎ |
3 |
フレーム溝にナットを組み込む際、力の入れすぎにより滑って溝に指が擦れ、けがをする。 |
○ |
4 |
組立て時の固定が甘いと、部品が外れて体に当たりけがをする。 |
◎:最重要危険ポイント/○:重要危険ポイント
3ラウンド:あなたならどうする?
上記の◎最重要危険ポイントに対して、以下の具体的対策案が提案されました。
※ |
1 |
手袋(使い捨て手袋は不可)を着用して組立てを行う。 |
|
2 |
組立前に部品の状態を確認し、大きなバリが出ていないことを確認する。 大きなバリがあれば除去してから組み立てを開始する。 |
※:重点実施項目
4ラウンド:私たちはこうする!
上記の対策案を実施するために、以下のチーム行動目標と指差し呼称を設定しました。
チーム行動目標 |
アルミフレームを組立てる際は、手袋を着用し作業を行う。 |
指差し呼称 |
手袋 よし! |
2024年12月の第1製造部(古川工場)の5S活動事例を紹介します。
第1製造部では「スノコ置き場見直し」を実施しました。
<改善前の状態&問題点>
包材などの下に敷くスノコの置き場は、第1ミーティングルーム前のシート裏ですが置き場がわかりにくく、また屋外保管のためスノコが汚れる状態でした。
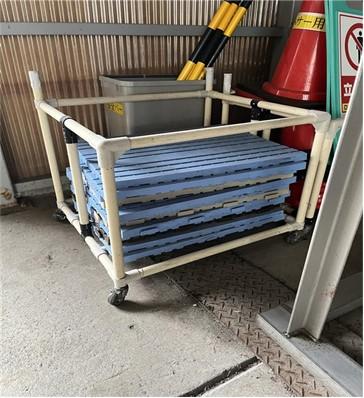
<改善後の状態&効果>
F棟通路入り口の空きスペースをスノコ置き場にした事で、誰にでも分かりやすくなり、また汚れる事なく保管・管理が出来るようになりました。
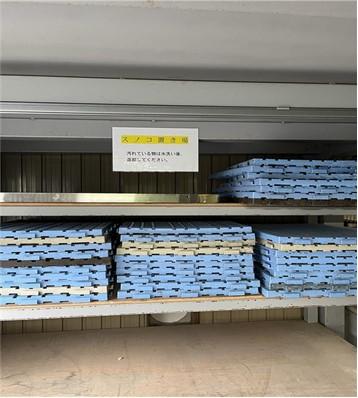
2024年12月の開発部(古川工場)の5S活動事例を紹介します。
開発部では「比表面積測定装置(BELSORP MINI X)備品収納」を実施しました。
<改善前の状態&問題点>
比表面積測定装置に用いる細かい部品は収納場所が無く、装置周辺の机の上に裸置きされている状態であり、紛失や埃の付着によって汚れてしまう懸念がありました。
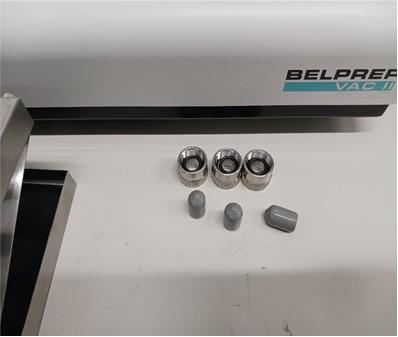
<改善後の状態&効果>
蓋つき容器に細かい部品を収納したことにより、紛失や埃によって汚れる心配がなくなりました。また、ラベルシールによって内容物を明記したことにより、収納場所が明確になり収納しやすくなりました。
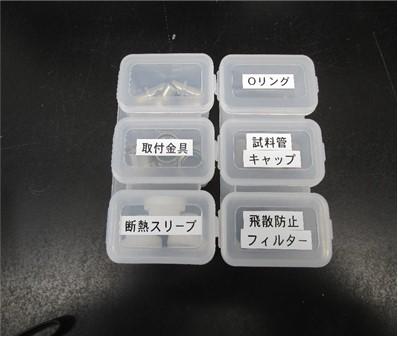
2024年12月の開発部(古川工場)の5S活動事例を紹介します。
開発部では「強度試験片作製用の型 乾燥カゴの改善」を実施しました。
<改善前の状態&問題点>
強度試験片作製用の型は細かい部品があり、乾燥機の網の下に落ち、汚れたり紛失する可能性がありました。また乾燥するときに容器から溢れてしまい、見た目が良くありませんでした。
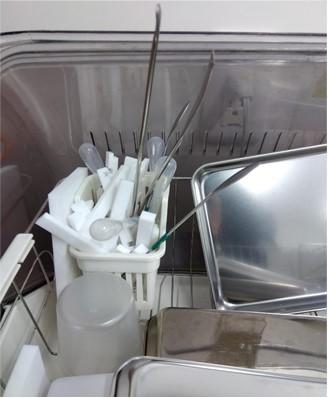
<改善後の状態&効果>
130×130(mm)、目開き1㎜のカゴを用いて、部品を乾燥することにより、乾燥機の網の下に落ち、汚れたり紛失する可能性が低くなりました。また、網の下に落ちた部品を拾う手間がなくなり、作業性が良くなりました。また、カゴから溢れることが無くなり、見た目が良くなりました。
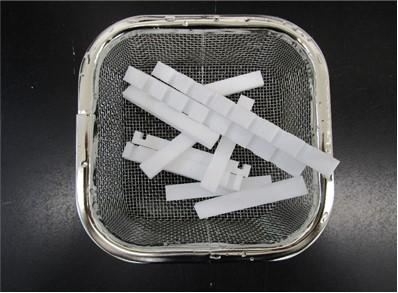
2024年12月の第2製造部(古川工場)のKY活動事例を紹介します。
以下の作業をテーマとして取り上げ、KYT(危険予知訓練)を実施しました。
テーマ
400型ターボミルのジャケット開閉作業
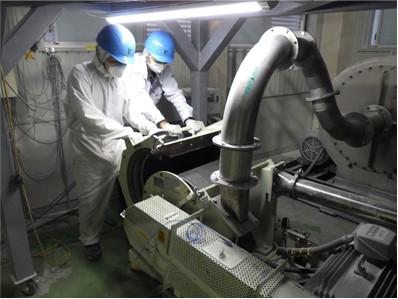
1ラウンド:どんな危険が潜んでいるか?
2ラウンド:これが危険ポイントだ!
以下の危険が挙げられ、重要危険ポイントを設定しました。
○ |
1 |
作業スペースが狭いため、ジャケットを開けた際に壁や架台とジャケットに挟まり怪我をする。 |
○ |
2 |
ジャケットは重量物のため無理な態勢で開閉を行うと腰を痛める。 |
|
3 |
ジャケットを開く際、持つ位置が悪いと床に着くときに手を挟み怪我をする。 |
|
4 |
ジャケットを開いた際、ゆっくり降ろさないと足を挟んでしまい怪我をする。 |
○ |
5 |
ジャケットを閉める際、勢いをつけ持ち上げようとすると腰を痛める。 |
◎ |
6 |
2人の息が合わないと片方の作業者に負担がかかり思わぬ事故につながる。 |
|
7 |
ジャケットを閉める際に指を挟んで怪我をする。 |
◎ |
8 |
足元に物が散乱しているとジャケットを開ける際、物に躓きジャケットと一緒に転倒し怪我をする。 |
◎:最重要危険ポイント/○:重要危険ポイント
3ラウンド:あなたならどうする?
上記の◎最重要危険ポイントに対して、以下の具体的対策案が提案されました。
|
1 |
掛け声をかけながら開閉作業を行う。 |
※ |
2 |
足元を整理し、作業スペースを確保してから行う。 |
※:重点実施項目
4ラウンド:私たちはこうする!
上記の対策案を実施するために、以下のチーム行動目標と指差し呼称を設定しました。
チーム行動目標 |
ジャケットを開閉する際は、作業スペースを確保し2人作業で行い掛け声をかけながら作業しよう。 |
指差し呼称 |
足元よし!! 準備よし!! |
2024年11月の原料部(古川工場)の5S活動事例を紹介します。
原料部では「階段下 備品置き場の整理・整頓」を実施しました。
<改善前の状態&問題点>
ペットボトル、空き缶入れや備品等を階段下に保管しているが、定置管理されていない為、取り出しにくく、見た目も良くない状態でした。
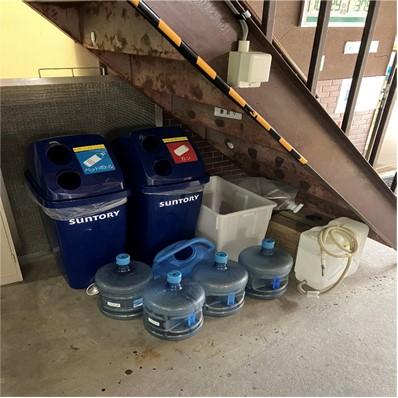
<改善後の状態&効果>
備品等、定置管理し不要なものを整理しました。 見た目もスッキリし必要なものを取り出しやすくなりました。
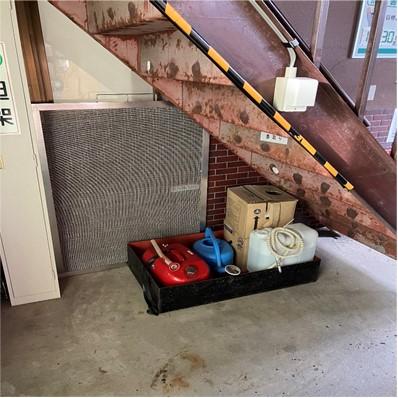