2023年7月の総務部(古川工場)の5S活動事例を紹介します。
総務部では「封筒保管の改善」を実施しました。
<改善前の状態&問題点>
社員への書類配付用の封筒は、個人名付き角2サイズのものを2種類使用している。当初は仮置きとして段ボールに片付けていたが、使い勝手も見た目も良いとは言えず、入りきらない部分が曲がってしまう状態だった。
<改善後の状態&効果>
封筒が収まるBOX型のミーティングバッグに変更した。中に可動式の仕切りがあるため、封筒の折れ曲がりがなくなった。また、持ち手が付いているため持ち運びが容易になった。保管時にはバッグの中に入れたものを表示できるため、保管内容も分かり易くなった。
2023年7月の原料課(古川工場)の5S活動事例を紹介します。
原料課では「原料フレコン積載用台車表示の改善」を実施しました。
<改善前の状態&問題点>
原料フレコンを載せるキャスター付きの台車にA(室)、B(室)の表示があったが端に小さく表示されているためわかりづらく間違えて使用することがありました。
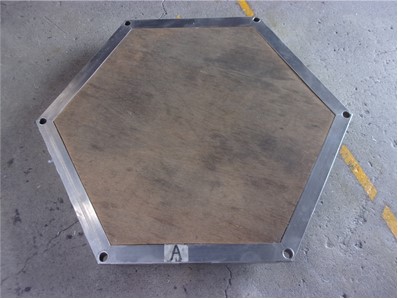
<改善後の状態&効果>
台車の真ん中に違う色でA、Bとスプレーで表示を行いました。一目でどちらの部屋の台車かわかるようになり間違えて使用することがなくなりました。
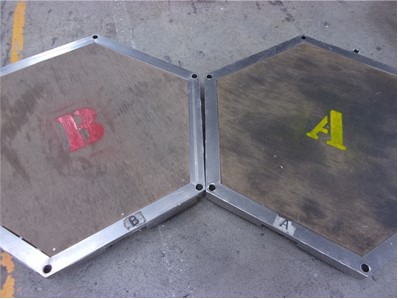
2023年6月の品質保証部(本社)の5S活動事例を紹介します。
品質保証部では「品質保証部事務所椅子」を実施しました。
<改善前の状態&問題点>
品証部事務所は狭い為、移動する時椅子がしっかり収納されていないと椅子の脚に引っ掛かり転びそうになってしまいます。
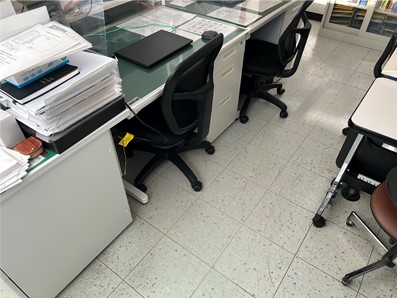
<改善後の状態&効果>
椅子を机の中にしっかり納めるよう、ラインを引きました。ラインの中に椅子を収めることではみ出しがなくなり、移動する時引っ掛かることがなくなりました。
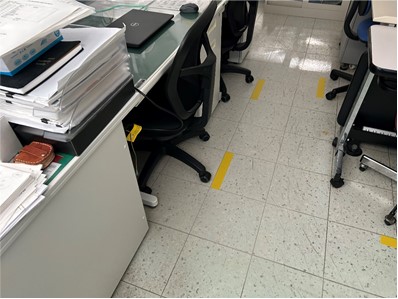
2023年6月の品質保証部(古川工場)の5S活動事例を紹介します。
品質保証部では「漏斗台使用時の液漏れを防ぐ」を実施しました。
<改善前の状態&問題点>
改善前の試薬の濾過台は、蓋が透明でない為、濾過された液が見えにくく、ピッチャーから液が溢れる可能性がありました。
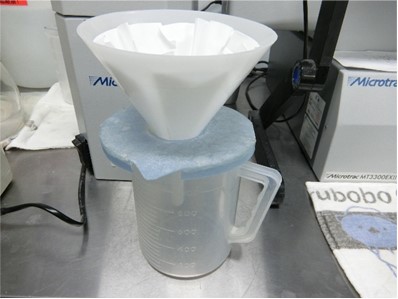
<改善後の状態&効果>
専用の漏斗台を購入したことにより、ピッチャーの液が見やすく、溢れる可能性がなくなりました。
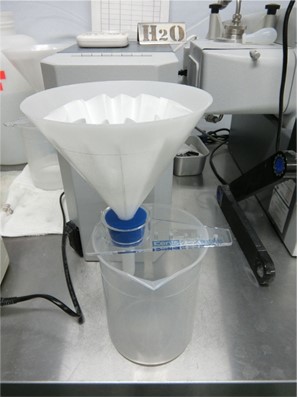
2022年6月の製造部(本社)の5S活動事例を紹介します。
製造部では「第3工場掃除道具置き場の改善」を実施しました。
<改善前の状態&問題点>
第3工場にある掃除道具は、特定の収納場所が決まっておらずフック等で引掛けておくだけの状態となっていました。
<改善後の状態&効果>
工場内の壁に掃除道具ごとのキャッチャーやフック取り付け、決められた場所に収納できるようにしました。定置管理され道具も収納しやすく整理整頓された状態となりました。
2022年4月の第2製造部(古川工場)の5S活動事例を紹介します。
第2製造部では「梱包用具置き場の設置」を実施しました。
<改善前の状態&問題点>
製品梱包をローラー台を使用して行う際、テープカッターや、ウエス、PPタイの置き場がありません。その為、不要なファイバードラムを利用し置き場として使用しています。
<改善後の状態&効果>
ローラー台に、ステンレス製で梱包用具を置ける台を設置しました。設置した事により作業効率が向上した事と、ローラー台の上部を有効活用出来るようになりました。
2021年12月の設備保全部(古川工場)の5S活動事例を紹介します。
設備保全部では「パンチング作業シート」を実施しました。
<改善前の状態&問題点>
パンチング作業台にはゴム製のシートが敷いてありますが、すぐに穴が空いてしまう為、パンチの刃先が壊れ交換の頻度が多かったです。
<改善後の状態&効果>
専用のシートに交換した事で穴が空き難くなった為、パンチ交換する頻度が減り、見た目も良くなりました。