2018年6月の品質保証部(古川工場)の5S活動事例を紹介します。
品質保証部では「物流作業時のバインダー定置管理」を実施しました。
<改善前の状態&問題点>
日常に於いて、入出荷に伴う物流業務は関係書類をバインダーに綴じて作業を行っていますが、これまでは座席の横に置いた状態でフォークリフトを運転していました。そのため、落下による書類の汚れやバインダーの破損などがありました。
<改善後の状態&効果>
座席の横にバインダーを収納できる様にトレイを設置しました。これにより、落下の心配もなくなり、書類がバインダーから外れて紛失することも無くなりました。
2018年6月の原料課(古川工場)の5S活動事例を紹介します。
原料課では「フッ素原料ラベル保管ケースの種類細分化」を実施しました。
<改善前の状態&問題点>
フッ素原料ラベルの収納スペースが少なく複数の種類のラベルがまとめて管理されていたため、片づけたり使用する際、間違えてしまう事がありました。
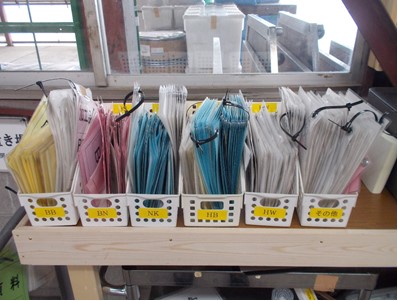
<改善後の状態&効果>
収納スペースを拡張しラックの数を増やしました。これによりすべての種類のラベルを個々に収納できるようになったため、使用、収納する際に間違えることが無くなりました。
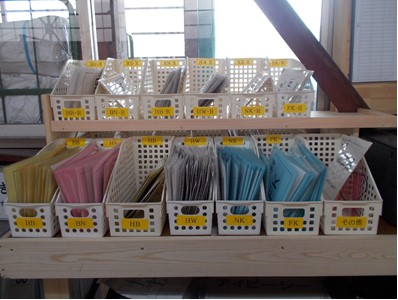
2018年6月の総務部(古川工場)のKY活動事例を紹介します。
以下の作業をテーマとして取り上げ、KYT(危険予知訓練)を実施しました。
テーマ
廃プラ保管作業
1ラウンド:どんな危険が潜んでいるか?
2ラウンド:これが危険ポイントだ!
以下の危険が挙げられ、重要危険ポイントを設定しました。
◎ |
1 |
廃プラを架台へ載せようとして、リフトの操作に気を取られ周りの作業者に気づかず接触する。 |
○ |
2 |
廃プラをリフトで架台へ載せようとして、架台の中までパレットを入れないと落下する。 |
◎ |
3 |
廃プラを架台へ載せた後、落下防止バーをつけ忘れると廃プラが落下する。 |
◎:最重要危険ポイント/○:重要危険ポイント
3ラウンド:あなたならどうする?
上記の◎最重要危険ポイントに対して、以下の具体的対策案が提案されました。
※ |
1 |
リフトで架台へ乗せようとする時は、周囲に作業者がいない事を確認する。 |
※ |
2 |
架台の中までパレットがしっかり入っているか確認し、落下防止バーをセットする。 |
※:重点実施項目
4ラウンド:私たちはこうする!
上記の対策案を実施するために、以下のチーム行動目標と指差し呼称を設定しました。
チーム行動目標 |
周囲に作業者がいない事を確認してから架台の上に置き、落下防止バーをセットする。 |
指差し呼称 |
周囲確認ヨシ!落下防止バーセットヨシ! |
2018年6月の第1製造部(古川工場)のKY活動事例を紹介します。
以下の作業をテーマとして取り上げ、KYT(危険予知訓練)を実施しました。
テーマ
回収機運搬、組み立て作業
1ラウンド:どんな危険が潜んでいるか?
2ラウンド:これが危険ポイントだ!
以下の危険が挙げられ、重要危険ポイントを設定しました。
◎ |
1 |
回収機をフォークリフトで運搬する時、段差などの衝撃で回収機がリフトのツメから滑り落ち、歩行者や周囲の人に当たりケガをする。 |
◎ |
2 |
回収機をフォークリフトで持ち上げる時、扉をしっかり閉めていないと開閉部のヒンジが曲がり、バランスが崩れ落下し、歩行者や周囲の人に当たりケガをする。 |
◎ |
3 |
回収機を組み上げる時、フォークリフトのツメの先端を上げて持ち上げないと回収機上部が滑り落ち、周囲の作業者に当たりケガをする。 |
○ |
4 |
回収機をフォークリフトで作業室から搬出する時、作業室の扉や壁に引っ掛かりバランスを崩して落下し、周囲の作業者に当たりケガをする。 |
◎:最重要危険ポイント/○:重要危険ポイント
3ラウンド:あなたならどうする?
上記の◎最重要危険ポイントに対して、以下の具体的対策案が提案されました。
※ |
1 |
回収機運搬用のステーとフォークリフトのツメをシャコ万でしっかりと固定をする。 |
|
2 |
回収機の扉のハンドルロックをしっかり閉めてから持ち上げる。 |
※:重点実施項目
4ラウンド:私たちはこうする!
上記の対策案を実施するために、以下のチーム行動目標と指差し呼称を設定しました。
チーム行動目標 |
回収機を運搬、組み立てする時は、扉のハンドルロックを閉めて、ステーとフォークリフトのツメをしっかりとシャコ万で固定してから行おう。 |
指差し呼称 |
扉よし! シャコ万よし! |
2018年6月の製造部(本社)のKY活動事例を紹介します。
以下の作業をテーマとして取り上げ、KYT(危険予知訓練)を実施しました。
テーマ
回収機設置作業
1ラウンド:どんな危険が潜んでいるか?
2ラウンド:これが危険ポイントだ!
以下の危険が挙げられ、重要危険ポイントを設定しました。
○ |
1 |
床に工具等が落ちていると作業者が踏んでしまいバランスを崩し転倒して怪我をする |
○ |
2 |
架台を移動させている時、回収機に取り付けていたシャコ万が落ちて作業者に当たり怪我をする |
○ |
3 |
架台を移動させる際、床が濡れていると足を滑らせ転倒し怪我をする |
|
4 |
架台を移動させる際、うまく架台が停止せず作業者が架台や設備にぶつかり怪我をする。 |
◎ |
5 |
架台を移動している時、周りにいる作業者に気が付かずぶつけてしまい怪我をさせる |
◎ |
6 |
架台を移動している時、周りの設備に作業者が身体をぶつけてしまい怪我をする |
◎:最重要危険ポイント/○:重要危険ポイント
3ラウンド:あなたならどうする?
上記の◎最重要危険ポイントに対して、以下の具体的対策案が提案されました。
※ |
1 |
作業前に、周囲をよく確認する |
|
2 |
作業前に、足元を確認し必要な場合は整理整頓清掃を実施する |
|
3 |
作業時は、保護具を着用する |
※:重点実施項目
4ラウンド:私たちはこうする!
上記の対策案を実施するために、以下のチーム行動目標と指差し呼称を設定しました。
チーム行動目標 |
架台を移動させる際は、保護具を着用し周囲や足元をよく確認してから作業しよう! |
指差し呼称 |
保護具着用・周囲・足元確認ヨシ! |
2018年4月の技術部(古川工場)の5S活動事例を紹介します。
技術部では「ダンボールシート保管方法の改善」を実施しました。
<改善前の状態&問題点>
塗装時や機械の下に敷くダンボールシートは紐でまとめ、床に直置きしてあり、移動させる時や、棚に収納してある物を持ち出す際に邪魔でした。
<改善後の状態&効果>
ワイヤーカゴとキャスター台車を合わせ専用の収納カゴを作りました。移動可能にしたことにより、ダンボールシートの取り出しも、収納棚からの部品取り出しも容易になりました。
2018年4月の第2製造部(古川工場)の5S活動事例を紹介します。
第2製造部では「デジタル顕微鏡の保管方法改善」を実施しました。
<改善前の状態&問題点>
設備の点検にデジタル顕微鏡を使って確認することがありますが、顕微鏡は精密機械なので出しっぱなしにもできず、使用後はそれぞれの箱に戻すという手間がありました。
<改善後の状態&効果>
緩衝材を入れた専用のケースを作りました。点検・測定の時はこのケースだけを持っていけばいいので使用や片付けの手間が減りました。