古川工場の架台置き場をアスファルト舗装しました。
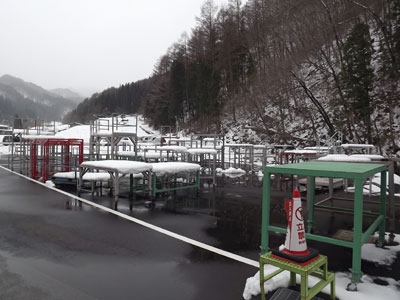
当社の製造現場では多くの架台を使用しますが、使用しないときは屋外に保管しています。写真の場所は以前は舗装されおらず砂利のままでした。
架台を運搬する際にはフォークリフトを使用するので、アスファルト舗装されたことで、今までよりも安定走行が可能となり、安全に架台の運搬ができるようになりました。
喜多さんの進化抄録集 : 喜多さんの進化
古川工場の架台置き場をアスファルト舗装しました。
当社の製造現場では多くの架台を使用しますが、使用しないときは屋外に保管しています。写真の場所は以前は舗装されおらず砂利のままでした。
架台を運搬する際にはフォークリフトを使用するので、アスファルト舗装されたことで、今までよりも安定走行が可能となり、安全に架台の運搬ができるようになりました。
古川工場に自動床洗浄機を導入しました。
当社では数年前から、工場内の粉砕室、通路、倉庫の床に防塵塗装を施してきました。この防塵塗装のおかげで、粉が床に舞い落ちても掃除がしやすい環境となっており、作業者は時間を見つけてはモップでさっと床掃除をして、綺麗な状態を保つことが習慣となっています。
この床掃除をもっと効率化するために、今回、自動床洗浄機を導入しました。
一品番の粉砕が終わった後などは、粉砕設備が解体され粉砕室から一掃されるので、この自動床洗浄機が見事に力を発揮し、モップよりも綺麗にスピーディーに床を掃除をすることができるようになりました。
スキマ時間にはモップ、広範囲を一度に掃除するときには自動床洗浄機、両方をうまく使いながら工場内を綺麗に保つようにしています。
「粉を扱う工場なのに、粉がぜんぜん落ちていませんね。」
工場にいらっしゃった方には、このように言っていただけるように常日頃、床掃除には気を配っています。
古川工場に高所作業リフターを導入しました。
古川工場には従来から高所作業車はありましたが、高所作業車を使用するには特別教育を修了していなければならず、使用できる者が限られていました。
今回、導入した高所作業リフターは自走せず人の手で移動させる方式であり、特別教育を受講する必要がありません。そのため、高所作業をしたい人が自ら持ち出してすぐに使うことができ、今までよりも効率的に作業を進めることができるようになりました。
古川工場の品質保証部製品管理課に「マワールでんラッパー」を導入しました。
マワールでんラッパーとは、パレットに積み上げた製品を半自動でシュリンク包装できるストレッチ包装機です。
導入の主な目的は、作業者の腰痛を予防することです。
マワールでんラッパーを導入する前は、作業者がシュリンクフィルムの筒を持って、積み上げられた製品の周囲をぐるぐると何周か歩いて回って包装していました。このとき、中腰の状態で歩いて回らなくてはならず、作業者の腰に負担がかかっていました。多いときには一日に30パレット以上のシュリンク包装をしているので、腰への負担は小さくはありませんでした。
導入したマワールでんラッパーは、ペダルを踏むことで、ターンテーブルに載せたパレット、製品を自動で回転させることができます。そのため、作業者はシュリンクフィルムの筒を持って中腰で歩き回る必要がなくなり、腰への負担は非常に小さくなりました。
古川工場に検査結果照会システムを導入しました。
検査結果照会システムとは、品質保証部で製品検査した結果を、作業担当者が製造現場の近くにいながら照会、確認できるシステムです。
検査結果照会システム
喜多村の製品検査では、検査の性質上または他品番の検査終了待ちが発生したりするため、検査結果が出るまでに時間を要することが多々あります。そのため、製造現場の作業担当者は検査結果が出るころを見計らって、品質保証部に確認しに行ったり、検査結果が出たあと検査員が現場へ伝えにいっていました。製造現場から品質保証部までは少し距離があるため、その間を往復する時間がムダになっていたり、作業を中断することで時間をロスしていました。
検査結果照会システムの導入に伴い、第一製造部(A棟、E棟の2箇所)と第二製造部(ミーティングルーム前)の計3箇所にタッチパネル式大型モニターが設置されました。モニターには製品毎の検査結果がリアルタイムで表示されますので、品質保証部で検査結果が出るとすぐにモニターで確認できます。タッチパネル式のため、操作も容易です。
作業担当者は、現場の近くにいながら検査結果をリアルタイムで確認することができるようになり、作業中断や往復する時間のムダを減らすことができています。
また、モニターには警告灯が付属しています。製品検査で規格外の結果が出て不合格になったものがあると警告灯が点灯し知らせる仕組みになっており、不合格に対してより敏感に察知できるようになっています。
警告灯
システム導入後、製造現場の作業者には非常に好評なため、モニターを4台追加設置することが決まっており、製品検査結果の伝達、確認がますますスムーズになることが期待されます。
なお、当社の基幹システムは業務開発部企画室がすべて社内開発しており、今回の検査照会システムも基幹システムの一部として開発しました。
原料課敷地内の土場をアスファルト舗装しました。
アスファルト舗装後の様子
これまでは砂地に定期的に砂利を入れて利用していましたが、トラックの走行や冬季の除雪によって砂利が少なくなると、強風の日などには砂埃が舞い、近隣にお住まいの方にはご迷惑をかけていました。また、原料課工場内にも砂埃が舞い込んできたりしていました。
雨の日の後には水はけが悪く、フォークリフトのタイヤに泥・砂が付着するため、工場内に入る前にはタイヤを毎回洗う必要があり、ムダな時間が生じていました。
今回、アスファルト舗装したことにより、上記のような砂埃や泥の問題は解消されました。
7月にご紹介しました本社製造部の「粉砕室のカーテンを防音仕様に/騒音対策を拡充!」に続き、本社製造部で実施した騒音対策をご紹介します。
下の写真は今回工場内に設置した防音シートです。
設置された防音シート
防音シートのこちら側は、近隣住宅に近い方であり、こちら側への騒音は出来る限り小さくする必要があります。
防音シートの向こう側には、騒音源となるコンプレッサーや粉砕機が稼働しており、非常に大きな音を発しています。以前はコンプレッサーのまわりだけ防音シートで囲って対策していましたが、それでは不十分だという会社判断により、粉砕機も含めて防音シートで囲うことにしました。
防音シートの効果は大きく、シートのこちら側の騒音は小さくすることができ、近隣住民への影響も小さくなったと思われます。