喜多村では5S活動の一環として「配線を上に」という活動をしています。
「配線を上に」とは、数年前から全社的に展開している改善活動で、今まで粉砕室の床に這っていた電気関係の配線を、宙に浮かせて設置しようというものです。
粉砕室では原料の投入時や製品の充填時に、少なからず粉が舞ってしまい、その粉が床面に落ちてしまいます。配線が床に這っていると、落ちた粉を取り除くための清掃に手間がかかり、綺麗な状態を保つのが困難な部分があります。
「配線を上に」することで、粉砕室の床面の清掃をしやすくし、粉砕室を常に綺麗な状態に保てるようになります。
本社、古川工場とも順次、「配線を上に」の工事を実施しており、いずれはすべての粉砕室の床から配線をなくす計画で改善を進めています。
本社製造部の設備部品洗浄用の水道・流し台を改修しました。
改修前はタイル張りの古い流し台で、冷水温水の調整もしずらい水道蛇口でした。
今回の改修で写真のような水道・流し台になり、作業者にとっては以前よりも清潔で使い勝手のよいものとなりました。
古川工場に新しいドラムプレス機を導入しました。
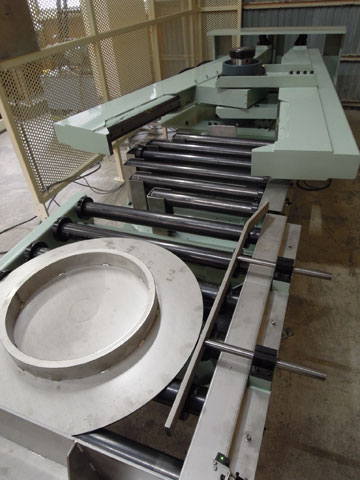
受託粉砕の中には、ドラム缶に原料を入れて送っていただくお客様もいます。ドラム缶内は液体原料を注入して冷えて固形状となった原料で満たされています。そのため、ドラムプレス機でドラム缶を押し潰し、中の原料を荒く砕いて取り出す必要があります。
ドラム缶一個につき、潰す箇所の高さや向きを変えたりして数カ所押し潰しますが、今までのドラムプレス機では押し潰す回数分、ドラム缶をセットし直していました。
今回新たに導入したドラムプレス機は、その工程を自動でやってくれます。ドラム缶をセットして一度ボタンを押せば、高さ向きも自動で変えてプレスしてくれるため、人の手間は大きく減りました。
また、ドラム缶をセットして安全柵を閉めてからでないとプレス機は作動しない安全装置も組み込んだため、作業者の安全性が今までよりも確保できています。
作業者の手間を削減し、安全を確保し安心して作業できるようにしたことで、お客様の製品の品質向上に繋がればよいと考えています。
本社工場に設備洗浄用の電気温水器を導入しました。
弊社の受託粉砕では一製品毎、粉砕設備を分解して洗浄します。今まで本社工場では、部品など小さなものはお湯が出る洗い場で洗浄していましたが、回収機など大型の粉砕設備用の洗い場では給湯器がなく年中冷たい水で洗浄していました。
今回、大型の粉砕設備用の洗い場でもお湯が使用できるように電気温水器を導入しました。
冬の寒い時期の作業者の負担を軽減するだけでなく、お湯で洗うことで回収機などに残留している粉体を速やかに洗い落とすことができ、作業効率の向上にも繋がっていきます。
10月に「消臭殺菌装置を実験的に導入/効果を確認中です!」という記事を掲載しました。
その消臭殺菌装置に関連して、エアーサンプラーを導入しました。
当社の受託粉砕では食品添加物の粉砕も受注しており食品添加物専用の粉砕室があります。
その粉砕室内で真菌等を発生させない対策のひとつとして消臭殺菌装置を導入し、今回のエアーサンプラーで空中浮遊菌をサンプリング、測定して殺菌装置の効果を確認しています。
2013年9月に本社工場の屋根を張替えました。それに伴い屋根の下には遮熱シートも設置しました。
本社工場の屋根は設置から何十年と経っていたため、劣化していて雨漏りの可能性がある部分もありました。今回の張替えではそういう部分もなくなり、安心して工場内で作業できるようになりました。
また、本社工場は夏期、非常に高温となって作業者の負担になっていました。これを少しでも改善するために、屋根の下に遮熱シートを設置しました。設置した以降に暑い日もありましたが、工場内の気温は以前よりも抑えられていました。作業者も効果を感じることができ、暑い時期の負担軽減に繋がりました。
屋根には採光口も設置したため昼間の工場内は今までよりも明るくなり、遮熱シートによる気温上昇抑制とともに場内環境の改善になりました。
2013年8月から製造現場での問題収集に「マンダラチャート」を取り入れました。
マンダラチャートとは、3×3の合計9マスの中央にテーマとなる言葉を入れ、その周囲の8マスにテーマに関連する事柄、問題点などを入れていくというアイデア発想法です。
喜多村では中央に製品名等をテーマとして入れ、その周りの8マスに「粉砕、分級、投入、回収、充填、保管、検査・測定、その他」という項目をあらかじめ設定しています。各項目の周りにさらに8マス用意されており、それをすべて埋められるように問題をどんどん発見していきます。
このマンダラチャートを製造現場で活用することで、積極的に問題を発見しようという意識が高まっています。今までは見えていなかった問題も徐々に見えてくるようになっています。
マンダラチャートの活用も含め、現場での問題発見力を向上させるよう努めています。