2024年7月の総務部(古川工場)のKY活動事例を紹介します。
以下の作業をテーマとして取り上げ、KYT(危険予知訓練)を実施しました。
テーマ
道路沿いの草刈りと補助作業
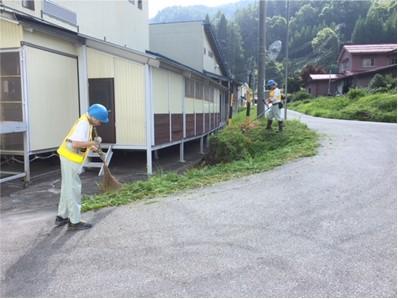
1ラウンド:どんな危険が潜んでいるか?
2ラウンド:これが危険ポイントだ!
以下の危険が挙げられ、重要危険ポイントを設定しました。
◎ |
1 |
道路沿いの草刈りと補助作業時は、作業に没頭していると通行車両が作業者に気付くのが遅れ、接触しケガをする。 |
◎ |
2 |
草刈り作業者と補助作業者の距離が近いと、回転刃が補助作業者の体に当たりケガをする。 |
◎ |
3 |
草刈り作業者と補助作業者の距離が近いと、小石が飛び跳ねて補助作業者の体に当たりケガをする。 |
◎ |
4 |
草刈り作業者は地面を見ながら作業をする為、電柱等の障害物に気がつくのが遅れ刈払い機をスライドさせた時、障害物に接触する。 |
○ |
5 |
草刈り作業者は地面を見ながら作業をする為、歩行者に気がつくのが遅れ小石が飛び跳ねて歩行者に当たりケガをする。 |
◎:最重要危険ポイント/○:重要危険ポイント
3ラウンド:あなたならどうする?
上記の◎最重要危険ポイントに対して、以下の具体的対策案が提案されました。
※ |
1 |
道路沿いの草刈りと補助作業をする時は、確実に安全反射ベストを着用して作業する。 |
※ |
2 |
草刈り作業者と補助作業者は8m程度の距離をとり、作業中は距離間を保つ。 |
※ |
3 |
草刈り作業開始前に、障害物がどこにあるのかを確認しておく。 |
※:重点実施項目
4ラウンド:私たちはこうする!
上記の対策案を実施するために、以下のチーム行動目標と指差し呼称を設定しました。
チーム行動目標 |
障害物を確認し、安全反射ベストを着用し、2人の距離間を保ちながら作業しよう。 |
指差し呼称 |
障害物確認ヨシ! ベスト着用、距離間ヨシ! |
2024年6月の製造部(本社)の5S活動事例を紹介します。
製造部では「清掃用品の置き場改善」を実施しました。
<改善前の状態&問題点>
掃除機などで使う清掃用品を書庫で種類別に保管していましたが、袋に入れて吊るしてあるので落ちやすく取り出しづらい状態になっていました。
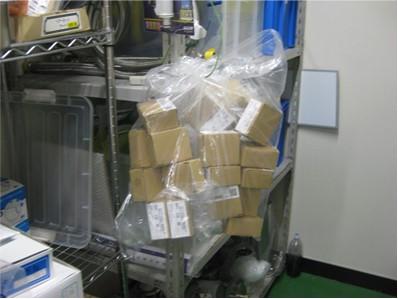
<改善後の状態&効果>
第一工場の工具室に清掃用品の置き場を移して保管するようにしました。スライドできる引き出しや長いボルトを利用して吊り下げて保管できるようになったので取り出しやすく整理整頓された状態になりました。
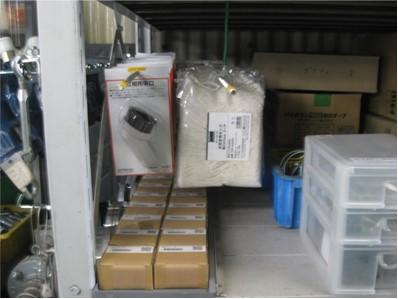
2024年6月の製造部(本社)の5S活動事例を紹介します。
製造部では「第2工場特殊工具置き場改善」を実施しました。
<改善前の状態&問題点>
第2工場で使用する特殊工具ですが、使用する頻度が少ない為ツールBOXに保管されいました。様々な物が入っており取り出しづらく不要な物も一部入っている状態になっていました。
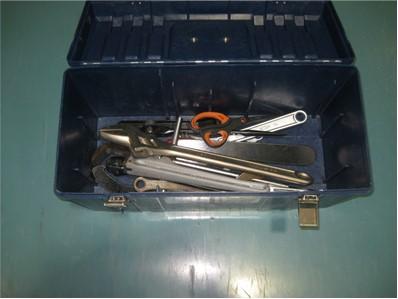
<改善後の状態&効果>
必要な特殊工具だけを選定し、既存の棚にフックを取り付け吊り下げて保管できるようにしました。余分な物が無くなり取りやすく整理整頓された状態となりました。
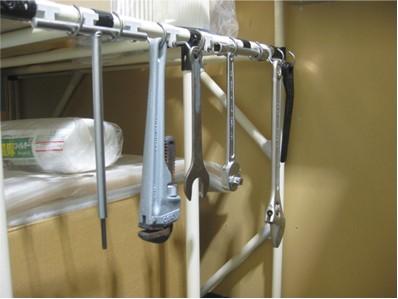
2024年6月の品質保証部(古川工場)の5S活動事例を紹介します。
品質保証部では「薬包紙のケース管理」を実施しました。
<改善前の状態&問題点>
秤で試料を量る時に使う薬包紙をケースに入れていましたが、蓋が無い為、空気中に舞い上がった微粉等が付着し、汚れる可能性がありました。
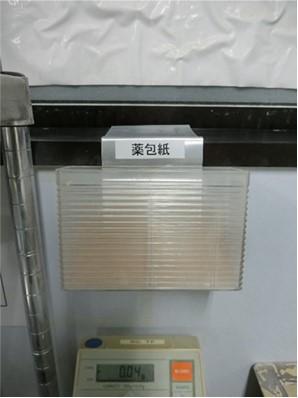
<改善後の状態&効果>
専用ケースを購入しました。専用ケースに変更した事により蓋が付いている為、微粉等の付着の防止ができました。

2024年6月の品質保証部(古川工場)の5S活動事例を紹介します。
品質保証部では「第三分析室エアコンクリーニング」を実施しました。
<改善前の状態&問題点>
第三分析室で使用しているエアコンが設置されてから数十年クリーニングされていない為、冷却効率が非常に悪く、電気代も余計にかかっていました。またフィンの部分に粉爆で舞い上がた粉が付着している為、匂いも臭い状態でした。
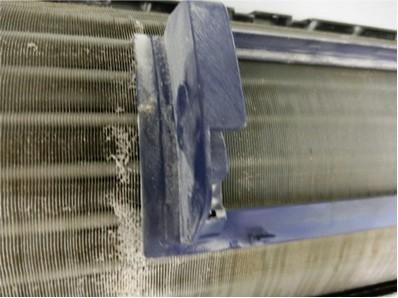
<改善後の状態&効果>
自前でエアコンクリーニングを行いました。 冷却スピードが格段に速くなり、臭い匂いもなくなった為、快適に作業することが出来るようになりました。
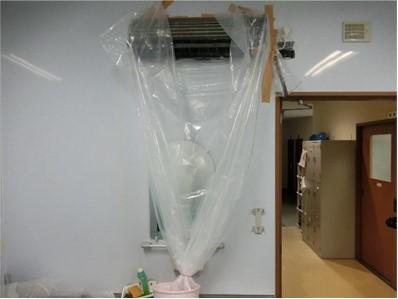
2024年6月度の第2製造部(古川工場)のKY活動事例を紹介します。
以下の作業をテーマとして取り上げ、KYT(危険予知訓練)を実施しました。
テーマ
3棟裏架台置き場からの架台運搬作業
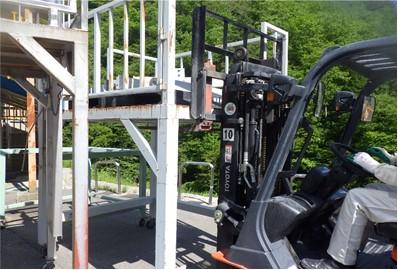
1ラウンド:どんな危険が潜んでいるか?
2ラウンド:これが危険ポイントだ!
以下の危険が挙げられ、重要危険ポイントを設定しました。
◎ |
1 |
各架台にはキャスターが取り付けられている為、架台を運搬し終わった際にキャスターをロックしないと架台が動いてしまい他の作業者に接触しケガをする。 |
◎ |
2 |
目当ての架台を持ち出す際に近くにある架台がキャスターロックしてないと架台が勝手に動き始め、他の作業者に接触しケガをする。 |
○ |
3 |
架台置き場付近は運搬用のトラックが出入りする事がある為、運搬する際に周囲を確認しないとトラックと接触しフォークリフトやトラックの運転者がケガをする。 |
○ |
4 |
架台置き場には傾斜がついている為、安全を確認せずにフォークリフトから降ろすと架台が動き周囲の作業者に当たりケガをする。 |
◎:最重要危険ポイント/○:重要危険ポイント
3ラウンド:あなたならどうする?
上記の◎最重要危険ポイントに対して、以下の具体的対策案が提案されました。
※ |
1 |
架台を運搬し終わった際は、キャスターを確実にロックし架台が動かないかをしっかり確認する。 |
※ |
2 |
架台を持ち出す際は、周囲の架台のキャスターが確実にロックしてあるかをしっかり確認する。 |
※:重点実施項目
4ラウンド:私たちはこうする!
上記の対策案を実施するために、以下のチーム行動目標と指差し呼称を設定しました。
チーム行動目標 |
架台の返却時または、持ち出す際はキャスターが確実にロックしてあるか確認しよう。 |
指差し呼称 |
キャスターロックよし! |
2024年6月の設備保全部(古川工場)のKY活動事例を紹介します。
以下の作業をテーマとして取り上げ、KYT(危険予知訓練)を実施しました。
テーマ
ベアリングヒート作業
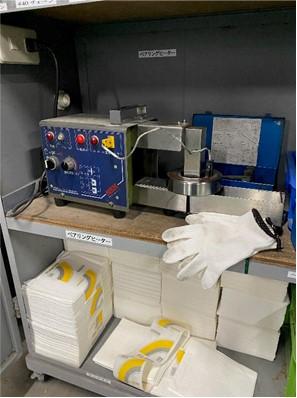
1ラウンド:どんな危険が潜んでいるか?
2ラウンド:これが危険ポイントだ!
以下の危険が挙げられ、重要危険ポイントを設定しました。
◎ |
1 |
素手でベアリングに触れると高温の為、火傷する。 |
◎ |
2 |
熱に弱い素材の手袋で作業すると手袋が溶け火傷する。 |
|
3 |
ベアリング運搬時、周囲を把握していないとベアリングを他の作業者に接触させ火傷する。 |
◎:最重要危険ポイント/○:重要危険ポイント
3ラウンド:あなたならどうする?
上記の◎最重要危険ポイントに対して、以下の具体的対策案が提案されました。
※ |
1 |
軍手を着用して作業する。 |
※ |
2 |
軍手を着用して作業する。 |
※:重点実施項目
4ラウンド:私たちはこうする!
上記の対策案を実施するために、以下のチーム行動目標と指差し呼称を設定しました。
チーム行動目標 |
ベアリングヒーター使用時は必ず軍手を着用して作業しよう! |
指差し呼称 |
軍手よし! |