2020年11月の第1製造部(古川工場)の5S活動事例を紹介します。
第1製造部では「脚立定置管理」を実施しました。
<改善前の状態&問題点>
C-1室配管置き場には脚立がありますが、すぐ使用できるように広げた状態で置かれていて、配管を取りに来た人は脚立に躓く可能性がありました。
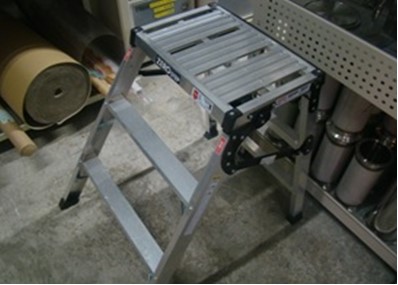
<改善後の状態&効果>
配管の棚にフックを取り付け表示をすることで定置管理が行えるようになりました。また、配管を取りに来た人も脚立に躓く可能性がなくなりました。
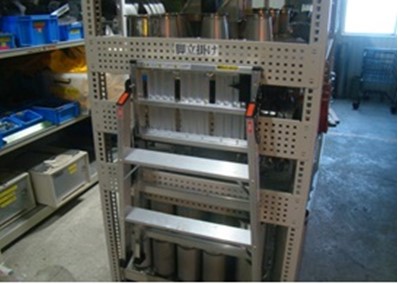
喜多さんの進化抄録集 : みんな de KAIZEN
2020年11月の第1製造部(古川工場)の5S活動事例を紹介します。
第1製造部では「脚立定置管理」を実施しました。
C-1室配管置き場には脚立がありますが、すぐ使用できるように広げた状態で置かれていて、配管を取りに来た人は脚立に躓く可能性がありました。
配管の棚にフックを取り付け表示をすることで定置管理が行えるようになりました。また、配管を取りに来た人も脚立に躓く可能性がなくなりました。
2020年11月の品質保証部(古川工場)のKY活動事例を紹介します。
以下の作業をテーマとして取り上げ、KYT(危険予知訓練)を実施しました。
ロータップ検査時の扉開閉作業
以下の危険が挙げられ、重要危険ポイントを設定しました。
○ | 1 | 扉を開ける時、他の作業者がいると扉が当たり怪我をする。 |
---|---|---|
○ | 2 | 扉を開けた状態で篩の出し入れをする時、他の作業者がいると接触し篩を足に落とし怪我をする。 |
◎ | 3 | 扉を閉める時、片手で取っ手を持って閉めると反対の手の指を挟み怪我をする。 |
○ | 4 | 扉を確実に閉めていないと、音が外に漏れ難聴になる。 |
◎:最重要危険ポイント/○:重要危険ポイント
上記の◎最重要危険ポイントに対して、以下の具体的対策案が提案されました。
※ | 1 | 扉を閉める時は必ず両手で取っ手を持って閉める。 |
---|
※:重点実施項目
上記の対策案を実施するために、以下のチーム行動目標と指差し呼称を設定しました。
チーム行動目標 | 扉を閉める時は必ず取っ手を両手で持って閉めよう! |
---|---|
指差し呼称 | 両手よし! |
2020年11月の設備保全部(古川工場)のKY活動事例を紹介します。
以下の作業をテーマとして取り上げ、KYT(危険予知訓練)を実施しました。
ボール盤穴あけ作業
以下の危険が挙げられ、重要危険ポイントを設定しました。
◎ | 1 | 顔を近づけすぎたり、肌を露出したまま作業すると切削屑が飛んで触り、火傷する。 |
---|---|---|
◎ | 2 | 保護めがねを使用せず作業すると切削屑が飛んで目に入り目を痛める。 |
○ | 3 | バイス固定が弱いと加工中、材料が外れ飛んで体に当たる。 |
◎:最重要危険ポイント/○:重要危険ポイント
上記の◎最重要危険ポイントに対して、以下の具体的対策案が提案されました。
※ | 1 | 加工部に近づき過ぎず、肌の露出も極力しないようにする。 |
---|---|---|
※ | 2 | ボール盤穴あけ作業を行うときは保護具を必ず着用する。 |
※:重点実施項目
上記の対策案を実施するために、以下のチーム行動目標と指差し呼称を設定しました。
チーム行動目標 | ボール盤穴あけ作業では、肌の露出を抑え、保護具を着用して作業しよう。 |
---|---|
指差し呼称 | 保護具ヨシ!火傷注意ヨシ! |
2020年11月の第2製造部(古川工場)のKY活動事例を紹介します。
以下の作業をテーマとして取り上げ、KYT(危険予知訓練)を実施しました。
製品缶吊り上げ作業(洗浄時)
以下の危険が挙げられ、重要危険ポイントを設定しました。
◎ | 1 | 製品缶の近くで操作を行うと、吊り上げた製品缶が自分や他の作業者の方に揺れて、接触し怪我をする。 |
---|---|---|
○ | 2 | シャックルの取り付けがあまいと操作中に外れ、落下してきた製品缶に接触し怪我をする。 |
3 | ベルトスリング付近に手を当てて操作すると手を挟んで怪我をする。 | |
◎ | 4 | キャスター付きの枠をロックし忘れて吊り上げると、枠が思わぬ方向に動き作業者に接触し怪我をする。 |
◎:最重要危険ポイント/○:重要危険ポイント
上記の◎最重要危険ポイントに対して、以下の具体的対策案が提案されました。
※ | 1 | 製品缶が揺れることを予測し、周囲に人が居ないことを確認してから離れて操作する。 |
---|---|---|
※ | 2 | キャスターをロックした後、製品缶が動かないことを確認する。 |
※:重点実施項目
上記の対策案を実施するために、以下のチーム行動目標と指差し呼称を設定しました。
チーム行動目標 | 製品缶吊り上げ作業を行う際は、キャスターのロックと周囲に人が居ないことを確認してから離れて操作しよう。 |
---|---|
指差し呼称 | キャスターロックよし!周囲よし!立ち位置よし! |
2020年10月の製造部(本社)の5S活動事例を紹介します。
製造部では「ホーロー(イモネジ)保管用ケースの作成」を実施しました。
工場内で使用するホーロー(イモネジ)はサイズの違う物が同じケース内で混在して保管してあり必要な物が取り出しずらい状態になっていました
仕切りのあるケースを使ってサイズ毎に保管できるようにしました。サイズが表示してあるので使用したい物が取り出しやすくなりました。
2020年10月の原料課(古川工場)の5S活動事例を紹介します。
原料課では「備品置き場の改善」を実施しました。
掃除用具置き場に手袋などを入れていて、とても狭く取り出しにくい。
作業場ロッカーの横に新たに備品置き場を設置しました。個人用の箱も大きいものに変更し取り出しやすく管理しやすくなりました。
2020年10月の第1製造部(古川工場)のKY活動事例を紹介します。
以下の作業をテーマとして取り上げ、KYT(危険予知訓練)を実施しました。
制御盤の運搬作業
以下の危険が挙げられ、重要危険ポイントを設定しました。
◎ | 1 | ラッシングベルトで固定をしていないと段差の衝撃や急操作でフォークから滑り落ち周囲の作業者に当たり怪我をする。 |
---|---|---|
◎ | 2 | ラッシングベルトの固定が確実にされていないと段差の衝撃や急操作でベルトが外れフォークから滑り落ち周囲の作業者に当たり怪我をする。 |
○ | 3 | 前進して運搬すると視界不良のため周囲の作業者に接触し怪我をする。 |
◎:最重要危険ポイント/○:重要危険ポイント
上記の◎最重要危険ポイントに対して、以下の具体的対策案が提案されました。
※ | 1 | ラッシングベルトによる固定が確実にされているか確認する。 |
---|
※:重点実施項目
上記の対策案を実施するために、以下のチーム行動目標と指差し呼称を設定しました。
チーム行動目標 | 制御盤の運搬作業はラッシングベルトの固定が確実にされているかを確認する。 |
---|---|
指差し呼称 | ベルト固定よし! |